NASA's Most Complex 3D-Printed Rocket Part Yet Passes Test (Video)
NASA has built two rocket engines with 3D-printed parts that are modeled after the same engines that could one day send humans on deep-space voyages beyond Earth. And these novel engines recently passed their first tests at the agency's Marshall Space Flight Center in Alabama.
While NASA has tested rockets with 3D-printed parts before, the two new rocket engines have the most complex 3D-printed components yet, the space agency says. Each rocket has a 3D-printed injector, and each one burned for five seconds and produced 20,000 lbs. (9,072 kilograms) of thrust during their tests in August.
"We wanted to go a step beyond just testing an injector and demonstrate how 3D printing could revolutionize rocket designs for increased system performance," Chris Singer, director of the Marshall Space Flight Center's Engineering Directorate, said in a statement. [Video: NASA Tests 3D-Printed Rocket Injector]
The 3D-printed injector, shoots propellant into the engine. An injector is complicated to build, but engineers can enter the design into a computer that then prints out the part by using a laser to fuse layers of metal powder together.
The advantage of 3D printing parts like an injector is that it requires only two pieces. Traditional manufacturing would require engineers to assemble a multitude of parts. In this case, a similar injector would require about 160 individual parts, NASA officials wrote.
Using 3D printing — also called additive manufacturing — also cuts down on the rocket's assembly time and production costs, NASA officials said in a statement. This kind of manufacturing makes more precise alignment possible and means the rocket will perform better and will be less likely to fail.
The injector is modeled after the RS-25 engine that powers NASA's Space Launch System rocket. The huge rocket is a heavy-lift, exploration-class rocket still under development, and space agency officials hope it will one day take humans to Mars.
Breaking space news, the latest updates on rocket launches, skywatching events and more!
Both rocket engines are designed to create complex flow patterns between oxygen and hydrogen that ignite and reach temperatures of up to 6,000 degrees Fahrenheit (3,316 degrees Celsius), according to a NASA description.
California-based Solid Concepts and Texas-based Directed Manufacturing each built one of the rocket injectors.
"We are working with industry [leaders] to learn how to take advantage of additive manufacturing in every stage of space-hardware construction, from design to operations in space," Jason Turpin, a propulsion engineer at the Marshall Space Flight Center, said in a statement. "We are applying everything we learn about making rocket-engine components to the Space Launch System and other space hardware."
Follow Kelly Dickerson on Twitter. Follow us @Spacedotcom, Facebook or Google+. Originally published on Space.com.
Join our Space Forums to keep talking space on the latest missions, night sky and more! And if you have a news tip, correction or comment, let us know at: community@space.com.
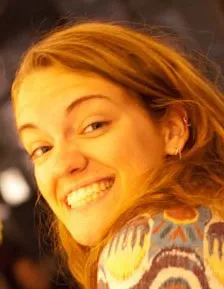
Kelly Dickerson is a staff writer for Live Science and Space.com. She regularly writes about physics, astronomy and environmental issues, as well as general science topics. Kelly is working on a Master of Arts degree at the City University of New York Graduate School of Journalism, and has a Bachelor of Science degree and Bachelor of Arts degree from Berry College. Kelly was a competitive swimmer for 13 years, and dabbles in skimboarding and long-distance running.