Clean, Quiet, Powerful: Engines for the New Jets
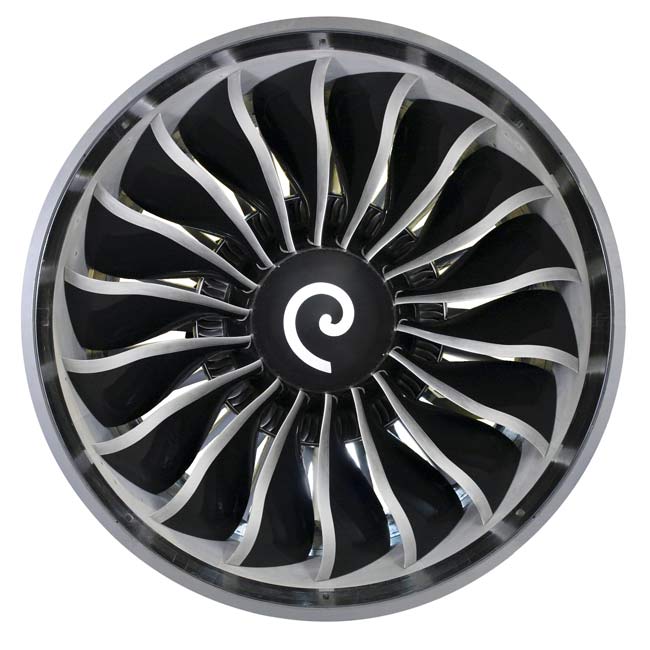
When theAirbus A380 and the Boeing 787 enter service, they will have the most advanced jetengines ever fitted to airliners.
GeneralElectric (GE), Rolls-Royce and the GE-Pratt & Whitney Engine Alliancerespectively have developed the GEnx for the Boeing 787; the Trent900 for the A380 and the Trent 1000 for the 787; and the GP7200 for the A380.
For itsfirst public appearance on Sunday and its first flight in September, the Boeing787 will have Rolls-Royce Trent1000 turbofan engines installed. The GEnx will featureon 787 deliveries starting in 2008. The Trent 900 and the GP7200 are alreadycertified for commercial service on the A380.
Since thelate 1960s, all Western commercial jet engines have been turbofans. Some 90percent of the thrust that today?s engines produce comes from cold air thatisn?t burned in the combustor at the engine?s core but is driven back at highsubsonic speed round the casing covering the center of the engine.
Manufacturerscall this ?bypass? air. It is produced by a huge fan at the front of the engine,which also sucks in the air that does enter the engine core. The air going into the core is compressed from atmospheric pressure to a pressure of 25 to 50 atmospheres, mixed with fuel and burned to drive the turbines that drive the fan and the compressors by means of steel spools.
Today?s bigturbofans have 10 to 14 turbine stages, each bearing dozens of blades. Theseengines generate so much thrust that every turbine blade handles as much poweras a Formula 1 racing car?s engine produces, said Robert Nuttall, vicepresident of marketing for Rolls-Royce?s Civil Business.
The latest enginesare much more environmentally friendly than earlier ones. The GEnx emits 15percent less carbon dioxide (CO2) than previous-generation engines forthe same thrust, said Melvyn Heard, marketing manager for the GEnx program.
Breaking space news, the latest updates on rocket launches, skywatching events and more!
It also produceshalf as much nitrogen oxides (NOx) as its forebears. NOx pollution is a particularconcern in communities near airports: High concentrations build up as jetengines idle for prolonged periods and then go to takeoff thrust.
Advances inaerodynamics and materials technologies allow new engine designs to weighsignificantly less per pound of thrust than earlier engines.
GEnx fanblades and the engine?s fan casing are made from composite materials, saving1,000 pounds of weight compared with previous-generation engines. This weightreduction improves the engine?s efficiency and fuel burn.
Rolls-Roycehas used superplastic-forming and diffusion-bonding techniques to createtitanium fan blades for the Trent 900 and 1000 that are hollow. These bladesare even lighter than composite fan blades but are just as strong as blades madeof solid titanium, said Nuttall.
Both manufacturersuse advanced nickel alloys covered with proprietary ceramic coatings to make high-pressureturbine blades, since these are the hottest parts of engines. The coatings actlike the ceramic tiles covering Space Shuttles, but are extremely thin.
The hottera jet engine runs, the more efficiently it produces thrust. So Rolls-Royce and GEhave designed their turbine blades to have lots of tiny holes. These holesforce relatively cool air on to the blade surfaces, allowing them to withstandhigher temperatures.
At 980degrees Fahrenheit, the cooling air for the turbine blades isn?t cool at all.But since it comes directly from the engine?s high-pressure compressor stages,it is much cooler than the air that exhausts from the combustor.
Today?s computersallow manufacturers to model the vastly complex fluid dynamics of air passingthrough a turbofan engine and to optimize every blade?s aerodynamic design. Thefan blades of the GEnx are so efficient aerodynamically that the fan only needs18 blades. GE?s predecessor engine needed 35.
Newpowerplants will be 50 percent quieter than today?s engines, thanks toinnovations such as the chevrons that Goodrich has designed for the787?s engine coverings, or nacelles. The scalloped chevrons look almost likehuge, regularly spaced bites out of the back of each nacelle.
Researchconducted by Boeing showed that chevrons efficiently mix bypass air exiting theengine with the outside air. This prevents the two air masses from shearingagainst each other to cause the hissing noise associated with jet engines.
Making fanblades from stronger and lighter materials also helps reduce engine noise. Fanblades can be made bigger to slow the tips of the blades below supersonicspeeds as they revolve. When the A380 and the 787 enter commercial service, almostall the noise the big airliners make will come from displacement of air by the airframes,not from the engines, said Heard.
The newpowerplants represent major technological achievements. But existing turbofanengines already do an amazing job.
?Theinternals of the engine are at half the temperature of the surface of the sunand the pressure at the center of the engine is equivalent to being half akilometer down in the ocean,? said Nuttall.
?Eachengine sucks in one and a half tons of air every second. They are constructedof 20,000 bits,? he said. ?And every engine has to operate for five years ormore without going into the garage.?
Join our Space Forums to keep talking space on the latest missions, night sky and more! And if you have a news tip, correction or comment, let us know at: community@space.com.
Chris Kjelgaard has more than 40 years of experience writing about and consulting on the civil aviation industry, aerospace and travel. He was a senior editor of Aviation.com from 2007-2008, and now works as a freelance writer and consultant in the aviation industry. He holds a B.S. in genetics from The University of Edinburgh.